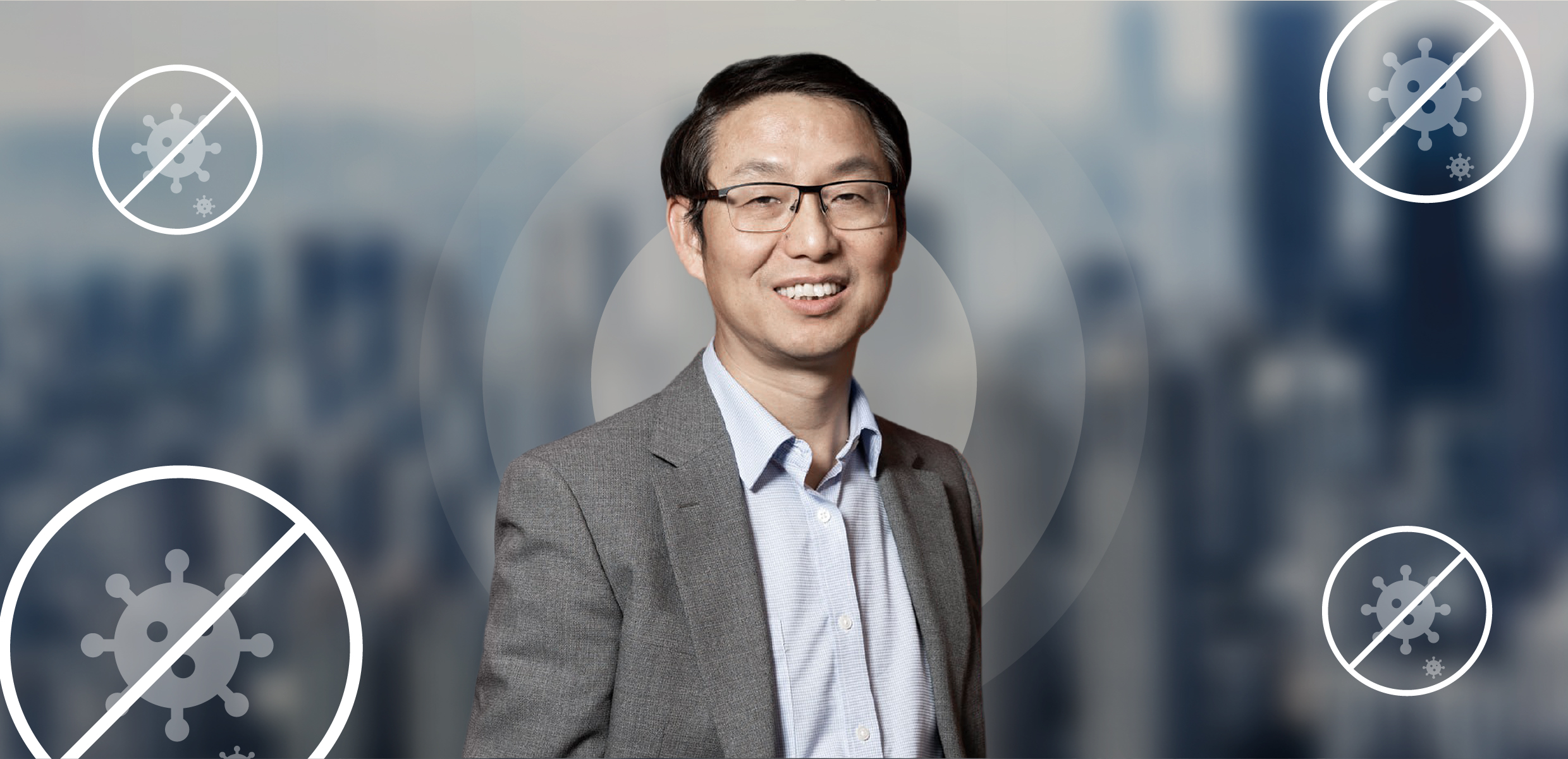
How can companies cope with Coronavirus? Lessons learnt from a multinational company operating in China
As the coronavirus crisis deepens, how can companies better react to such situations and better anticipate the end of the public health crisis? Bo Zhou, company founder and CEO of FuturMaster, a software editor specialising in supply chain planning solutions, sheds some light on the topic and shares the feedback from one of the world leaders in FMCG sector operating in China. With many of its clients in Europe worried about the impact on their supply chains, Bo Zhou, explains how manufacturers and retailers can limit or even avoid shortages.
The impacts on Chinese businesses, manufacturers and retailers:
The impact of the coronavirus has been huge to Chinese businesses. For one of FuturMaster’s beverage customers, sales in February were down 80 percent compared to last year. For another customer operating in fashion, it was only able to achieve about 30 percent of like-for-like sales thanks mainly to online, while physical stores were closed.
Following the lockdown, the volume and geographical distribution of demand drastically changed due to so many people being quarantined at home.
“During times of uncertainty, demand evolves in unexpected ways. In this context, every company needs to make simulations on how and if they can satisfy this demand based on their production and distribution capacity. You also need to closely monitor which transportation routes are cut and how many workers will be unable to show up at various sites due to lockdown. Unfortunately, many companies don’t have the technologies to support these simulations; so they’re unable to anticipate the impacts under different crisis scenarios,” said Zhou.
Food shortages and empty shelves:
Panic buying – many supermarkets have seen empty shelves from people buying up all the bottled water, hand sanitisers and toilet rolls – and further stock-piling by consumers are likely to test suppliers to the limit.
Companies are also seeing reductions in their production and distribution capacities due to labour shortages: for instance, when one worker tests positive to the Covid-19, the whole team can be put into quarantine.
Moving products around can turn out to be an issue as well, especially when transportation routes are affected due to border closures.
“Anticipating ahead – by doing simulations – enables companies to be better prepared. Being able to react in an agile and efficient way is vital for coping with the crisis on a daily basis.”
“During the crisis, companies need to produce more with reduced resources. They also need to produce more efficiently, that is to say produce only what is most in demand,” Zhou said.
Feedback from a multinational company operating in China
When the coronavirus epidemic erupted in China, Chinese companies faced exactly the same challenges. One of the world leaders in FMCG operating in China has been able to respond quickly to the emergency and avoid severe shortages thanks to using FuturMaster’s supply chain planning software solutions.
The company has numerous factories it can call upon based on forecasting of demand and the number of workers in each factory.
When the virus outbreak emerged in the country, the supply chain teams were able to determine which were the most important products to prioritise, by taking into account the stock on hand in each warehouse and the available production and distribution capacities.
When Wuhan and nearby towns went into lockdown, a team of planners were already preparing for various possible closures in different geographical areas. So it looked at the areas likely to be most affected and where else it could produce, and at what capacity. These planners monitored which transportation routes were cut, and by using the FuturMaster solution, were able to update their distribution network and know which city will be supplied by which factory.
The supply chain teams regularly collected information from local managers to understand how many workers were most likely to be available. It ran simulation after simulation. It came up with a plan A, a plan B, C, and so on. This foresight and planning meant that it was less likely to be taken by surprise and resulted in continued supplies to their clients.
The multinational company was able to endure the turmoil largely thanks to FuturMaster’s supply chain planning technology and the ability to model different scenarios and choose the best solutions “in real time”. For instance, by shifting production capacity to different locations to cope with factory closures and offset transportation problems, the company was able to produce and supply enough goods while controlling costs.
Advices to businesses to better cope with the crisis
“Everything that seems normal before the crisis becomes a challenge. All the variables that supply chain planners use on an everyday basis become uncertain and questionable. However, companies can reduce the impact of the current crisis by simulating and planning the supply chain “in real time”. The goal is to focus on the remaining capacities to produce efficiently while controlling costs,” said Zhou.
“Businesses can better react and better anticipate the end of lockdown by using supply chain planning solutions based on advanced optimisation capabilities. These technologies can help prioritise possible options whenever there’s a choice to be made and make better decisions afterwards.”
Bo Zhou, President and CEO, FuturMaster
Bo Zhou is the President of FuturMaster, a company he founded 25 years ago. FuturMaster provides supply chain planning software to over 500 customers in 90 countries, including Sanofi, Lactalis, Heineken and L’Oréal. He has taught in various business schools, such as ESCP Europe, CNAM and Paris Dauphine in France.
About FuturMaster
Providing artificial intelligence (AI) augmented supply chain solutions, FuturMaster helps clients achieve service excellence, growth in revenue and profit. More than 500 customers, representing over 10,000 users across 90 countries, trust FuturMaster to optimise their end-to-end supply chain (demand, supply and S&OP) and improve their business performance. With over 25 years of expertise, FuturMaster solutions have been deployed at global leaders in multiple industries, including Sanofi, Lactalis, Heineken and L’Oréal. Founded in 1994, FuturMaster has offices in France, the UK, Singapore, China and distributors in Germany, Australia and Brazil. www.futurmaster.com
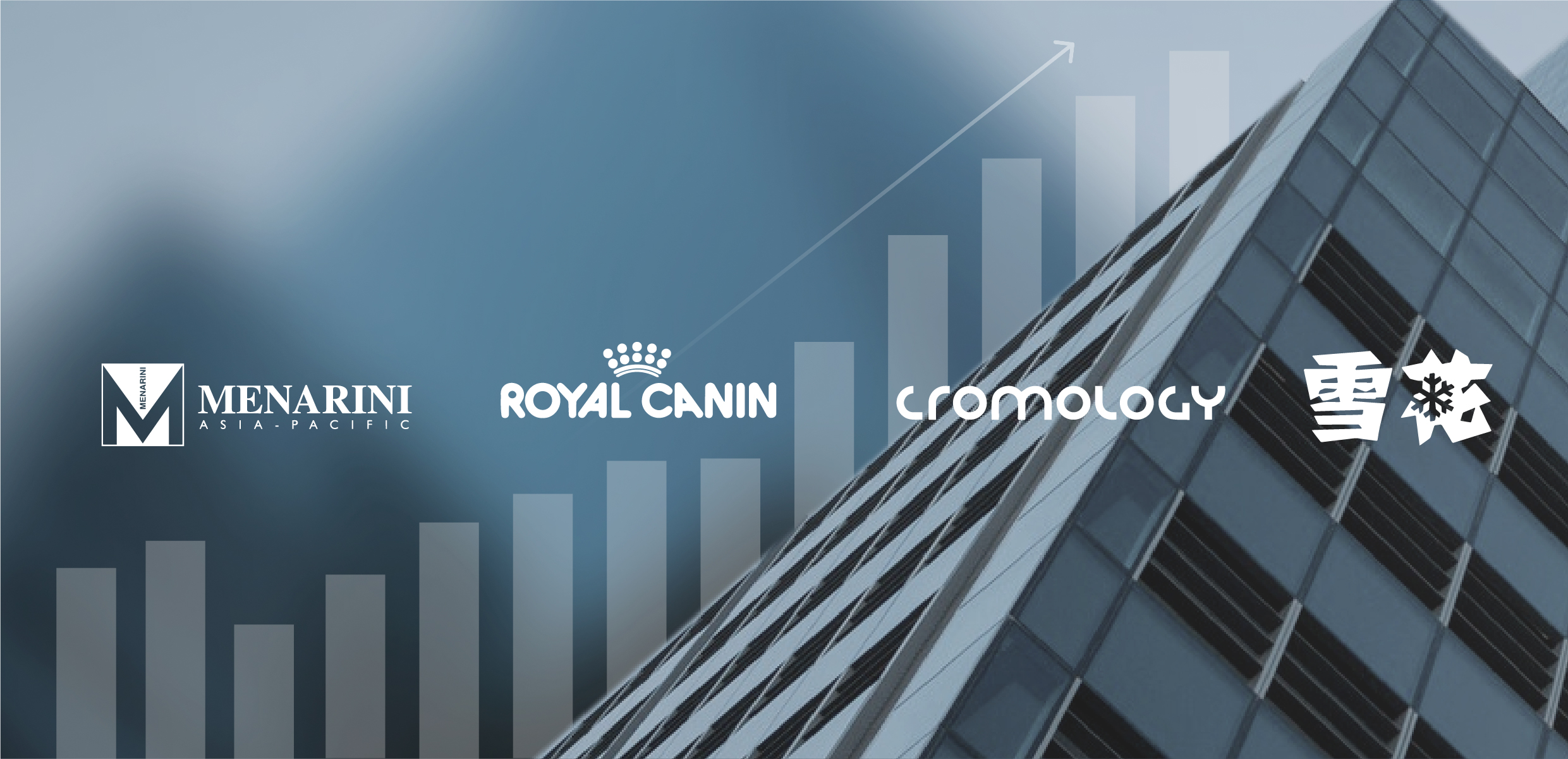
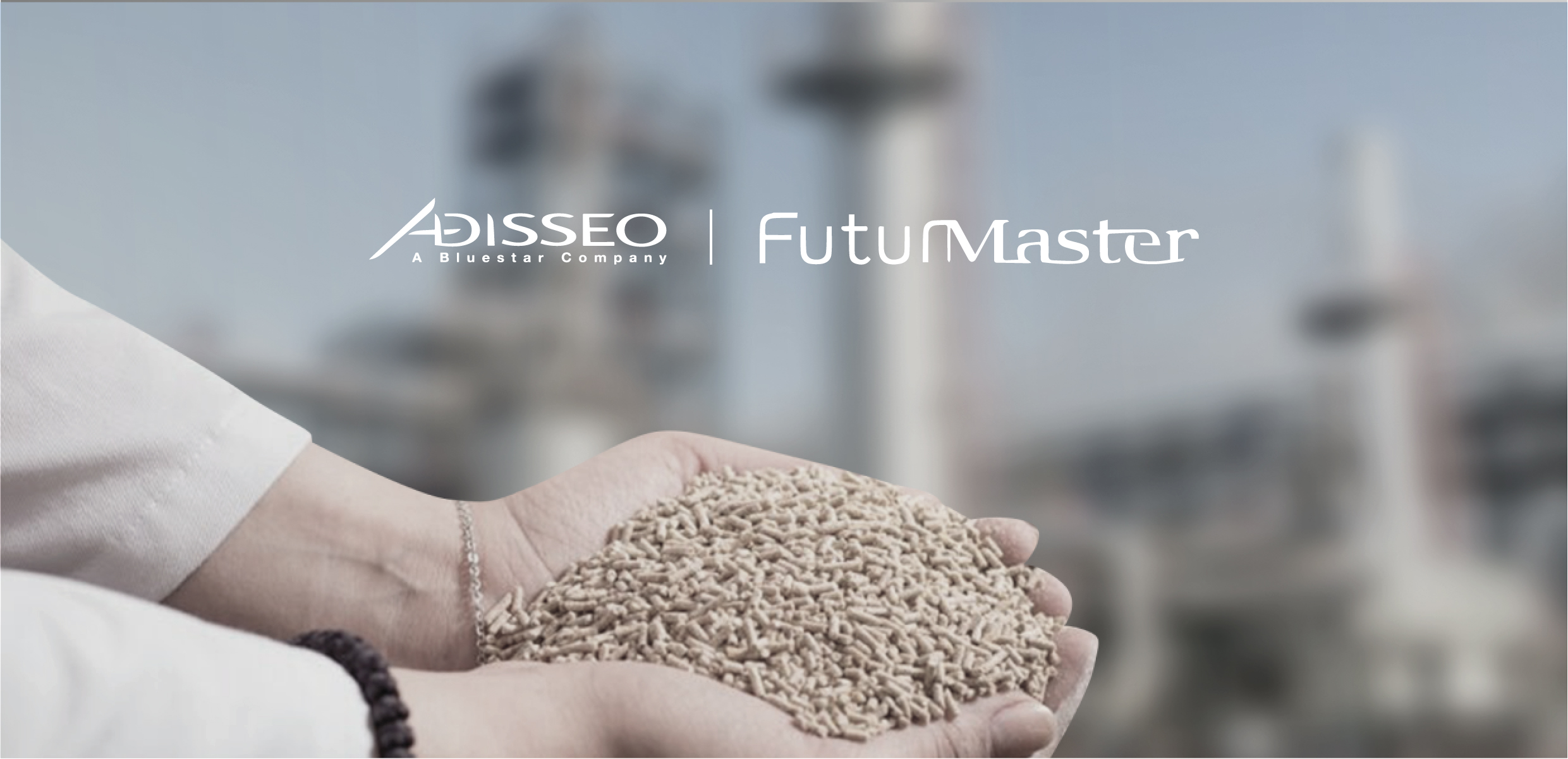